High productivity for stainless tanks
ESAB Shield-Bright cored wires pave the way to speedy quality welding
Patent Kft. is a Hungarian company that successfully survived the political and economic transformation by combining quality traditions with an easy acceptance of new, productive technologies.
ESAB is their preferred welding partner, appreciated for its customer orientated practical support. In 2009, ESAB assisted in the implementation of a productive process solution for the welding of stainless steel tanks – using Shield-Bright cored wires.
Patent Kft
Patent Kft started in 1989 with the production of stainless barrels and devices for breweries. Since then, their portfolio has expanded with tanks for the food (milk), chemical and pharmaceutical industries, pressure vessels, containers, silos and smaller vessels for power plants. From the beginning, the company aimed at the demanding Western European market, adopting high quality standards which formed the basis for current success. They are the dominant Hungarian company in their field of fabrication and enjoy an excellent reputation outside the country. A tight deadline for a new project – the construction of four 1500 m3 tanks for Hungary’s largest chemical company – resulted in a management decision to invest in the future by re-assessing the welding of stainless steel tanks, the objective being to drastically increase productivity.
A change in welding culture
It was clear from the moment Patent Kft received the order that their traditionally applied welding technology, manual and mechanised TIG welding, was far too slow to meet the requested delivery time and that it was the right moment to change to a more economical technology. With assistance and support from ESAB, management embarked on a revolution in welding culture.
After two decades of tradition in high quality TIG welding, a company like Patent Kft is steeped in TIG and abandoning it might be compared to quitting smoking. It was a massive challenge – as much for the management as for the employees.
ESAB’s stainless steel tank welding solution needed to cover the complete welding process – power sources, consumables, mechanisation and welding procedures. In addition, ESAB was asked to provide practical demonstrations and welder training.
Scope of welding tasks
The tanks, each with a diameter of 11m and a height of 16m, are made of 304L type austenitic stainless steel in 5, 6, 8, 10 and 12mm thickness.
They have 11 rings constructed from 1500 x 6000 mm sheets. First the roof is constructed, and lifted, after which the rings are fitted, one by one, from top to bottom, to form the shell. The welding of the shell involves 380 m of joints in the PC (2G) position and 100m in PF (3G) position, plus the joints in the roof and bottom plate. The tank welding tasks involved three areas: the bottom; the shell; and the roof.
Tank bottom
The bottom of the tank is constructed from 5mm thick, 6000 x 1500mm sheets. The sheets are bevelled to 60° butt joints and the root is welded onto 5 mm thick stainless steel strips. This bottom plate is welded onto a 12mm thick base ring by means of overlap joints, whereas the first tank ring is joined to the same base ring with two-sided fillet welds. These downhand butt, overlap and fillets welds are suitable for light mechanisation – ESAB’s Miggytrac 2000 welding tractor being a logical choice.
Less obvious was the selection of ESAB’s top- end digital power source, the AristoMig 5000iw with AristoPendant U8 control pendant and AristoFeed 3004w wire feed unit – where a less advanced power source would also have fulfilled the requirements for the complete tank. Patent Kft management opted for the AristoMig 5000iw, because its SuperPulse function in the U8 control unit could be applied to other projects. Very thin plate applications – a substantial part of the Patent Kft portfolio which was formerly covered by mechanised TIG -can now be welded with the faster MAG process making it possible to combine arc types and fully control the heat input. In this way, the company has a ‘work horse’ for heavy welds and, at the same time, a machine for precision welds.
ESAB advised Patent Kft to extensively test 1.2mm Shield-Bright 308L X-tra rutile cored wire for the downhand butt, overlap and fillet welds, convincing them that this consumable best met their high quality and productivity demands. This wire has been specially developed for applications in the PA and PB position, yielding high integrity welds at deposition rates as high as 10kg/h (Ar/2.5% CO2 shielding gas).
It allows Patent Kft to weld the butt and fillet welds in the tank bottom in one pass at a travel speed of 50-55 cm/min and a deposition rate of around 10kg/h (butt welds on stainless steel backing strip).
Tibor Patonai, Technical Manager: “Previously, we welded thicker plates in three runs, using synchronic TIG for the root (two welders welding the same joint, simultaneously), and the solid wire MAG process for the filler layers. With ESAB’s Shield-Bright on ceramic backing, we complete joints in one run; even when welding manually. Another advantage is reduced deformation as a result of the high travel speed and low heat input. In addition, we enjoy an extremely low defect rate with hardly any porosity, cold laps or slag inclusions. The Shield-Bright products became so popular in our workshop that even the proudest TIG welders volunteered to use the wire, in spite of their long time antipathy for the MAG process.”
Tank shell
The tank shell represents the majority of the welding work. During the planning stage, it was divided into two welding areas; the top segments (5 to 5mm, 5 to 6 mm, 6 to 6mm joints) and the lower segments (8 to 8mm, 8 to 10mm, 10 to 10mm and 10 to 12mm). All involve butt joints in the PC (2G) and PF (3G) positions. For the top segment, welds in PC position were carried out with solid wire MAG welding with 1.0mm OK Autrod 308LSi welding wire. Welds were performed in one run on FILARC PZ1500/87 ceramic backing with concave groove. Bevelling was not necessary and welds were absolutely free of defects – together bringing substantial time and cost savings. The PF welds were still welded with synchronised TIG, because there was not enough time to train the welders in the use of MAG welding with ESAB SuperPulse.
For the lower segment in thicker plate, multi-layer welds were performed with 1.2mm Shield-Bright 308L all positional rutile cored wire with fast freezing slag. It was applied in both manual (root runs in PF position) and mechanised welding (filler and cap layers).
The root procedure, however, differed for the PC and PF welding positions. Initially, economic root pass welds with Shield- Bright 308L in PC position on ceramic backing at a travel speed of 28 cm/min proved unsuccessful, because the necessary heavy tack welds could not be remelted completely. Also big fit-up and root gap variations played a role in insufficient root penetration. This was avoided by welding the root pass in PC position with solid wire on PZ1500/87 backing, but at a lower travel speed of 13-15cm/ min.
For the filling and cap layers, Shield-Bright 308L yielded high integrity welds at travel speeds of 40 and 60 cm/min, respectively.
In PF position, there were similar conditions for the root pass, but insufficient root penetration was not an issue because of the larger weld pool. The full joint was welded with ShieldBright 308L.
Shield-Bright benefits:
· Downhand and all-positional rutile · wires for austenitic stainless steel · Productive · Welder-friendly · Superb weld appearance · No pulse equipment needed · Ar/CO2 mixed gas and CO2 · Vacuum packed |
The root pass was done manually on FILARC PZ1500/71 ceramic backing with a rectangular groove. The fit-up tolerances did not allow for mechanisation in the filling and cap layer.
Tank roof
The roof grid (called the star by the welders), was pre-fabricated in the workshop and transported in one piece to the tank construction site. Most of the welding work could be brought in the downhand position to optimise benefit from the high deposition rate of ESAB’s ShieldBright 308L X-tra. The remaining positional welds were performed with ShieldBright 308L. After on-site connection of the star to the tank’s top segment, stiffener beams, cover plates and welded with the all positional ShieldBright.
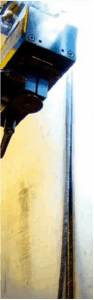
Figure 8. Shield-Bright 308L X-tra joint in pre-fabrication of the ‘star’
The Patent Kft partnership with ESAB is based on practical, result-orientated advice and support. Prior to the project, this took the form of local demonstrations, the joint evaluation of different solutions, the selection of the most suitable and effective welding technology and the establishment of welding procedures. This co-operation continued into the construction stage, where active support solved occasional problems. The co-operation was the basis for the successful construction of the four 1500 m tanks within a period of five months – well within the deadline required by the customer.
Mr. Tibor Patonai concluded, “ESAB’s approach is the most sympathetic in the marketplace. They do not press us to apply any standard technology, but actively help us to realise the solution that best meets our quality and productivity needs. Their flexible and helpful attitude was key to reaching our targets with this project.”
ESAB Launches Cutmaster Series of handheld plasma cutters
In May this year – ESAB Welding & Cutting Products announced the launch of its ESAB Cutmaster® Series of portable air plasma cutting systems, which range in output from 20 to 120 amps and produce a recommended “quality” cut on material from 6 mm to 40 mm. ESAB Cutmaster plasma cutters are among the lightest and most compact in the industry, making them highly portable and easy to store.
With ESAB Cutmaster products, the recommended cut capacity equals the system’s true cut capacity. A recommended cut has a smooth cut face with little or no dross and requires little or no rework or grinding, all of which improve productivity and quality. ESAB Cutmaster products provide additional output when needed, offering a maximum cut thickness that ranges from 60 to 150% greater than the recommended cut. As a result, they eliminate the concept of having to “buy up,” or purchase a machine larger than end-users actually need.
Four products in the ESAB Cutmaster Series (the 60, 80, 100 and 120) share common features. These include a tubular “roll bar” that protect the front and rear of the power supply for durability, as well as make the unit easier to carry. A trigger latch feature prevents hand fatigue during longer cuts, as it allows the operator to release the trigger while the system keeps cutting. Color-coded LEDs on the front panel indicate pressure status and setup errors. The Auto Pilot Restart feature instantly reignites the pilot arc while cutting expanded metals such as grates and chain link fences. Each unit comes standard with the industry-leading 1Torch (6.1 or 15.2 m cable options), but they also accept mechanised and automated torches.
For primary power and location flexibility, the ESAB Cutmaster 40 enables users to switch from 1-phase, 208 – 230VAC primary power to 110VAC primary.
This unit produces a genuine cut on 12 mm material, cuts a maximum thickness of 15 mm material and weighs only 11.8 kg.
The ESAB Cutmaster 60 features a 60-amp output, has a genuine cut of 20 mm and severance cut of 32 mm. It provides a 12 mm cut at 635 mm per minute, which is 25% to more than 100% faster than competitive models and weighs just 19.5 kg. This unit can also be used for medium duty gouging applications when fitted with the correct torch consumables.
The ESAB Cutmaster 80 features an 80-amp output, has a genuine cut of 25 mm and severance cut of 38 mm. It also weighs just 19.5 kg.
The ESAB Cutmaster 100 features a 100-amp output, has a genuine cut of 35 mm and severance cut of 45 mm and weighs 28.1 kg.
The ESAB Cutmaster 120 features a 120-amp output, has a genuine cut of 40 mm and severance cut of 55 mm and weighs 28.1 kg.
For primary power and location flexibility, the ESAB Cutmaster 40 enables users to switch from 1-phase, 208 – 230VAC primary power to 115VAC primary. This unit produces a genuine cut on 12 mm material, cuts a maximum thickness of 15 mm material and weighs only 11.8 kg.
ESAB Welding & Cutting Products is a recognised leader in the welding and cutting industry.
From time-honoured processes in welding and cutting to revolutionary technologies in mechanised cutting and automation, ESAB’s welding consumables, equipment, and accessories bring solutions to customers around the globe.
About the Author: Tamás Sándor, Mechanical Engineer, IWE Is product manager consumables at Esab, Hungary. He joined Esab In 2005.