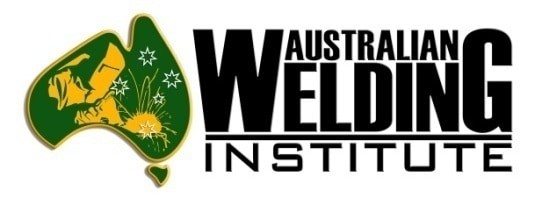
Training Opportunities – AWI Certification
January 1, 2014 in Welding Certification, Welding Supervisors
AWITM Certification is now available for Welding Supervisors
Streamlined, relevant and practical certification.
The Australian Welding Institute AWITM has been successful in introducing and running a program for AS 1796 Certifications 1 to 9. The AWITM is now extending the program to include Certifications 10 and Welding Supervisors to AS 2214.
The industry has been waiting for the return of a practical, relevant qualification, which is cost competitive to the WTIA.
Wait no longer, the AWITM are making this happen!
AWITM examination papers have been written and validated by industry experts that have extensive experience in the relevant disciplines.
Feedback from running the first round of examinations are exampled below:
‘they are based much more on what we need to know in the workshop’
and
‘it was a very detailed exam but based on practical application of being a supervisor’.
The AWITM has listened to key stakeholders – Industry, but more importantly -YOU – and have provided a certification system that measures the skills and knowledge of welding supervisors. For example, there will not be questions on MIAB or Laser welding in the exam. Instead, we have elected to use the examination period to focus on the more ‘relevant skills’.
EXAMINATION DATES 2013
to be held in all capital cities *based on demand
Friday 11th April 2013 Paper A
Saturday 12th April 2013 Paper B1 and B2
At the very least the examinations will be held in Adelaide and Perth, but other sites will be included based on demand.
If you would like to sit your examinations with the AWI, contact your local AWITM representative (details on back cover) or email admin@welding.org.au.
Application forms will be forwarded to you.
Your intention to sit for the examinations needs to be in by 21/3/14 with formal applications closing on 21/3/14.
‘Don’t expect it to be easy, AWITM is raising the bar on these important industry qualifications’
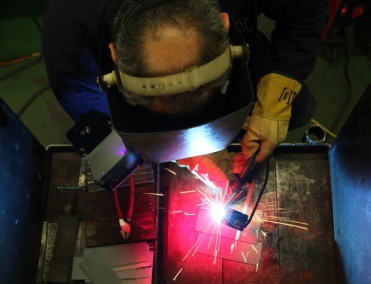
SMENCO – MeltView APEX
January 1, 2014 in Equipment
The MeltView APEX is an educational tool for demonstrating arc welding safely and effectively. Clearly show how to read the arc and weld puddle for GMAW, FCAW and GTAW. Teach more effectively and enhance knowledge transfer.
Benefits:
- Teach welders faster
- Enhance student understanding
- Increase qualification testing success
- Reduce training costs
Applications:
Manual welding demonstrations at
- Trade schools
- Trade shows
- Welding OEMs
- Welding distributors
- Manufacturers and fabricators
Features:
Versatile
- GTAW, FCAW and GMAW
- Variety of joint configurations
- Multiple positions
Adaptable
- Configurable accessories for recording, lighting, body position camera
Lightweight flexible mount for wide range of applications and views
Integrated protection including spatter shield and electrical insulation
Camera feeds directly into monitor; no computer required
Manual Welding applications
GTAW, GMAW and FCAW Butt and fillet joints
All welding positions
pipe and flat geometries
Project onto a monitor the view of the welder
- Arc length
- Arc column
- Tungsten shape
- Weld puddle
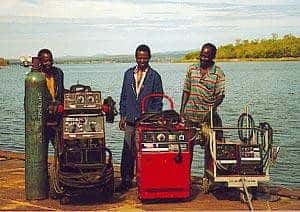
Lincoln Electric provides solutions
January 1, 2014 in Articles
How Lincoln Electric helped a small business grow in Zimbabwe
Graham Nell and his father own a small fishing operation situated on the shores of Lake Kariba in a remote area of Zimbabwe. Needless to say their aluminium pontoon boats were not easy to maintain – the nearest service station was 400 kilometres away. Fixing cracks in the boats seams was not a problem – as long as they had a generator. Hear in Graham’s own words how local authorized distributor Ron Cary of Graham Bates Services and Lincoln Electric helped two small business owners half way around the world to solve their welding needs and grow their business.
My father and myself started are small Kapenta fishing operation on Lake Kariba in the early 90’s at a place called Siamatalele, a remote area in Zimbabwe 400 kilometres from the second largest city in Zimbabwe, Bulawayo. “Kapenta” (or limdothrissa miodin), a small sardine, originally from Lake Tanganyika was introduced into Lake Kariba in 1967 and 1968 and has since become a staple part of the diet for the indigenous black Zimbabwean.
Kapenta is harvested at night from a pontoon with the use of a 7 metre circular net, suspended from a boom and lifted with a winch, driven off a stationary engine. Shoals of Kapenta are located with the use of echo sounders just before sunset. 400-watt mercury vapour lights are used to attract the Kapenta as well as an underwater light suspended above the net which runs down the net cable.
After a period of time, the overhead lights are switched off while the underwater light remains on. The net is then lifted hopefully loaded with silvery Kapenta. Lifts occur approximately every hour until sunrise. The fish lifted out of the net are mixed with a coarse salt and left in the wire baskets to drain. When the Kapenta rigs return to shore in the morning, the Kapenta are spread out on drying racks and sun-dried. Once dried they are packed.
The boats used in this operation are 13 meters x 1.2 meters – – twin pontoons with a deck area in between.
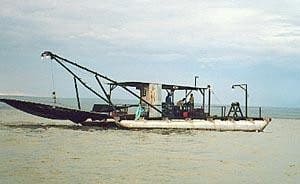
The Nells own a fleet of Kapenta pontoons. “Kapenta,” a small sardine, is a staple of indigenous Zimbabweans
This configuration of twin pontoons has proved the best for stability in the often stormy and rough waters experienced on the lake. They are driven by 40 HP outboard motors.
Originally we used steel pontoons fabricated in Bulawayo. These were then transported to our base on the lake some 400 kilometres away, and the rigs were then assembled right in the water. Although under normal conditions this may prove satisfactory at first, the repairs and maintenance to the steel structures of the pontoon are costly at hindsight, due to the incompatibility of salt, steel, and water, over a long period of time. Also, using steel pontoons becomes time-consuming as they have be taken out of the water for maintenance, either for repair, sandblasting, and repainting annually.
In view of the above difficulties, we made a decision to try aluminium pontoons in an effort to cut down on the maintenance. Sending damaged pontoons over to Bulawayo for repair was unpractical and out of the question.
We had our first set of experimental pontoons fabricated in Bulawayo. However, after a few months in operation, and although we had eliminated the problems of rust and corrosion, small cracks had appeared along some of the welded seams and gussets of the pontoon – possibly due to poor workmanship initially. Our workshop was in those days geared to steel pontoons and totally inadequate for repairs to aluminium.
Fortunately about this time my father recollected having seen Lincoln welding equipment being exhibited at the Zimbabwe International Trade Fair held in Bulawayo. We decided to find the Lincoln distributor there and this was the beginning of a firm friendship with Ron Cary, General Manager of the Welding Division of Graham Bates Services.
We discussed our immediate problems and requirements with Ron, and due to the other problem with only having generated power, Ron recommended the Lincoln Ranger 8 fitted with a TIG module. His reasoning being that we would not only be able to repair the aluminium pontoons currently in service with TIG, but also because the Ranger 8 has a broad range of AC and DC welding capabilities in stick, MIG, and TIG welding modes, and also generator combined – we would be able to weld steel as well as use the generator for power tools. This, combined with the fact that the machine was fully portable, were sufficient reasons to purchase this Ranger 8 welding package.
Ron personally delivered the Ranger 8 to our workshops in Siamatalele where he commissioned and instructed us and our mechanics/welders on the use and correct welding techniques of the Ranger 8.
However, a further problem arose when we had to cut aluminium plate for the repairs to our pontoons. Initial efforts with a hacksaw were time-consuming and ineffective, and while the use of steel cutting discs eventually did the job, it proved to be very costly in time and cutting discs. We decided to go back to Graham Bates Services to seek further advice from Ron once again. Ron suggested that, because of our remote location, and the problems we were experiencing, we needed to become self-sufficient with a setup where we could do all our cutting and repairing on site. He suggested a plasma-cutting machine and recommended the Pro- Cut 60. We purchased this unit and were immediately given a full demonstration and detailed instruction on its use and capability.
We now have four (4) operational aluminium Kapenta rigs with more under construction and one set of aluminium pontoons under repair. These pontoons are off a rig which was blown onto the rocks during a storm, and although badly damaged, the prospect of repairing them is not as daunting as it should be with the Lincoln welding equipment we now have at hand.
We were so impressed by the reliability and performance of our Lincoln Equipment and the personal service and backup provided by Graham Bates Services that the purchase of another two machines followed naturally. We now have an Invertec V250S welder which takes care of all my steel welding needs in the workshop, as well as a Lincoln SP140-1 which is extremely useful for light-gauge welding – impossible with most other stick welders.
At the end of the day, Lincoln has provided our Company not only with versatility, mobility, backup service and expertise, but has also made me truly self-sufficient – not easy to achieve for a small company operating in such a remote part of the world!
Thank you Ron – and thank you Lincoln.
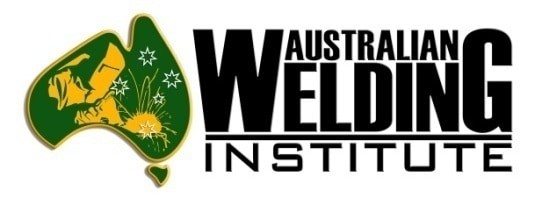
Training Opportunities
January 1, 2014 in Welding Certification
The AWI and TWI are joining forces
Courses to be run near you
Appreciation of Engineering Quality Documentation Review Course
Course Code: WIS 21
The AWI and TWI are joining forces to bring relevant course material to the industry. A course designed to assist those involved with welding quality but do not require the detailed knowledge of the welding coordinators course. The Appreciation of Engineering Quality Documentation Review program will be rolled out as a series of four which will be run around the country in 2014.
Dates / Venue 28th April WA
26th May Qld
18th August NSW
20th October SA
Duration 3 days
Cost $990 AUD
Course is suitable for:
Personnel involved in compiling and reviewing mechanical / engineering quality documentation for client acceptance. Inspectors, engineers, document controllers looking to expend their current knowledge of Quality Control activities.
Course content:
Analytical review of engineering documentation: material test certificates; Post Weld Heat Treatment; Visual, weld audit and weld history reports; fundamental knowledge requirements for QC personnel to carry out document review; in-depth assessment of documentation.
Course Objectives:
To be able to identify and quantify fabrication or procedural non-compliances against specified procedures.
Additional information:
Course entry is not restricted, however it is recommended that students have some knowledge / experience of the engineering / construction industry.
To register your interest contact AWI
admin@welding.org.au or michael.trinidad@twisea.com
Courses are run subject to numbers
Get qualified in 2014 – Eddy Current Testing (ET) now covers testing of tubes and aerospace
Kuala Lumpur 7 – 18 April 2014
Kuala Lumpur 3 – 14 November 2014
The course is ideal for all NDT personnel, inspectors and technicians responsible for, or engaged in, practical application of eddy current testing and writing techniques and instructions for detection of flaws in cast and wrought product, material identification/determination of properties, coating thickness measurement, tube testing and weld inspections.
Also suitable to personnel engaged in inspection of aerospace materials, components and structure.
Course Objectives:
To detect cracks, surface and near-surface, in aircraft components, structures, tubes and welds
To detect corrosion and thinning in non-magnetic materials
To grade and sort materials on the basis of conductivity and permeability
To write clear and concise inspection instructions and test reports
To meet the syllabus requirements of CSWIP/PCN Level 2
Examination of cast forged and wrought products or tubing such as that found in condensers, heat exchangers and air conditioning units. This course covers the techniques of surface inspection and/or internal bore inspection and is supported by examinations complying with BS EN ISO 9712.
The course ends with the certification examination.
Training in accordance with the requirements of ISO 9712.
TWI Technology (S.E.Asia) Sdn. Bhd., Malaysia
Tel: +603 61573526
Email: inquiry@twisea.com
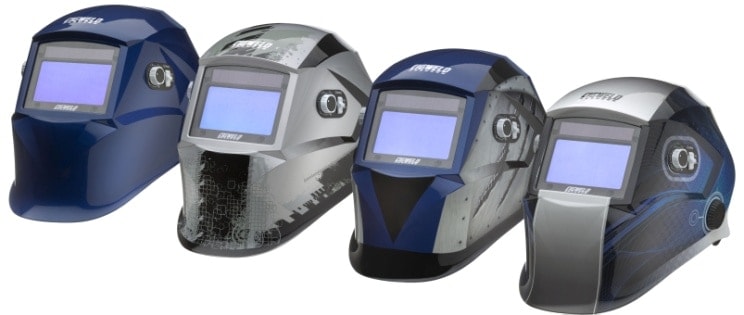
Cigweld – ProLite Helmets
January 1, 2014 in Equipment
Eye-viz protection
With so many different applications for welding and grinding, it pays to choose the right helmet for the job ~ Laura Carrazza, Marketing Manager at CIGWELD explains.
In Australia, welding and grinding are responsible for nearly a third of all eye injuries[1] and result in more than 500 hospitalisations every year.
Aside from the pain and inconvenience caused, that results in thousands of lost hours – as many as 26,000[2] by some estimates. For a busy construction or mining business, that’s a lot of downtime.
As you might expect, a lot of these injuries occur when people don’t wear protection. In a survey conducted by Monash University in Victoria[3], as many as half of those injured through welding related activities and a third of those injured through grinding related activities didn’t report wearing any eye protection at all.
But the fact remains that even with protection, far too many people are getting injured. Why? Because they’re relying on inappropriate or sub-standard equipment, or simply not using it properly.
The risks
When welding, the biggest risk is ‘flash’ or ‘arc eye’– a sort of sunburn to the cornea, caused by staring too long at harmful ultra violet rays (like arc light). Extremely painful and potentially debilitating.
When grinding, you must be wary of a disc spinning at 7,000-odd RPM or flying debris – normally hot shards of metal, which can easily be flicked underneath or through the sides of safety glasses and become embedded in the eye.
So how can you protect yourself when welding or grinding?
The right tools for the job
It’s critical to choose the right equipment and that means wearing a proper, fit-for-purpose welding helmet that not only protects your eyes but also offers full facial and neck protection – reducing the impact of arc rays that can cause burning of the skin.
One of the reasons welders get injured is because they remove their protection too early. If you’re welding for hours at a time, or you’re grinding in a hot and cramped environment, it’s crucial that you’re not itching to rip your helmet off the moment you’ve finished a weld. Look for something that:
- is comfortable and lightweight
- has a good sweatband to keep the sweat out of your eyes, and
- has a good field of view.
In short, look for a helmet that you’d feel happy wearing all day long.
To minimise injury and maximise the quality of your workmanship, you want to be able to focus on the job in hand.
Look for a helmet that:
- is compliant to Australian Standards
- is auto-darkening and has adjustable shade settings
- has a minimium of two light sensors, more premium helmets have 4 sensors that will respond with greater sensitivity to changes in light.
- has a minimum reaction time of 1/20,000th second
- is made of durable hardwearing material – ideally high impact rated if you are going to use it for grinding as well.
- ideally allows you to change between welding and grinding modes at the single push of a button
- has easily replaceable batteries and possibly even solar assist – to prolong battery life.
Cigweld. Helping you see the light
CIGWELD’s ProLite welding and grinding helmet was launched to market in Feb / Mar 2014 with four highly sensitive sensors, that can take readings and make adjustments to the variable lens in less than 1/20,000th of a second. Even at very low amperages, the helmet knows exactly how much light to let in, which makes it ideal for low current AC & DC TIG work as well as more powerful stick and MIG jobs.
The ProLite not only runs on regular, replaceable CR2450 lithium batteries. It features a clever solar panel which draws energy from the arc rays it’s exposed to and uses that to power up the lens – prolonging battery life in the process.
Vision is also improved with a generous viewing area of 98mm x 55mm, welding is not just easier – it’s more precise too. You can keep your head steady and your focus on the job in hand.
A simple button allows you to switch between welding and grinding modes, so you’re not plunged into darkness the moment you pick up your grinder. There’s an optional magnification lens too, which slots in easily to make light work of more fiddly jobs.
Best of all, unlike most other welding helmets on the market, the ProLite range is fully compliant with Australian Standards and the stringent requirements that are laid out in AS/NZS1337.1 & AS/NZS1338.1. This high impact rated helmet incorporates all the latest technology, while ticking all the safety boxes – so you can rest assured you’re getting a safe, practical and easy to use welding helmet from a brand you can trust!!
CIGWELD ProLite – fit for purpose
There is a huge range of welding applications in Australia, from heavy industry to agriculture, mining to car panelling – as well as amateur hobby work.
With such diversity, it makes sense to choose a helmet that is 100% fit for purpose – not a compromise for the sake of functionality, price or design.
- A TIG welder working on intricate joins, for example, is likely to want a helmet that works even at low amps.
- A boilermaker in the mines or out on an oil rig might be looking for something that offers maximum protection in a tough environment.
- If you work in a fab shop and spend all day behind a torch, comfort is possibly your main consideration.
- And if you’re running a small farm, you may be looking for durability and value for money.
The ProLite meets all the above requirements and is suited to your task at hand, whatever your specific needs. Keeping you and your colleagues safe is always the number one priority, that’s why it’s worth taking the time to find the best tool for the job. You’ve only got one pair of eyes after all …
New clean air products from Kemper
With a clear focus on innovation KEMPER has launched a new range of products. The new CleanAirTower is designed clean air indoors where local exhaust ventilation is not feasible and it is unique in the market.
The MaxiFil Clean is also a new addition to the KEMPER range, allowing for convenient portability and 360 degree operating radius. It includes many time saving features, like the on/off switch on the hood that ensure ease of use and maximum productivity while fully complying with safety standards.
KEMPER has been focused on clean air and safety in welding and cutting operations for more than 40 years. KEMPER extraction technologies offer excellent value for money at time of purchase and many use cleanable filters minimizing on-going costs.
KEMPER products come with a limited warranty and provide hazardous smoke and dust extraction during welding, cutting, or grinding. These OH&S compliant welding smoke removal products have won the respect of clients like Caterpillar, amazon.com, General Electric, Snapper, John Deere, Yamaha, IBM, and many more.
Large or small, KEMPER has cost effective solutions to suit any scale project.
Kemper is distributed nationally by SMENCO Pty Ltd, 1300 728 422 www.smenco.com.au
[1] http://www.monash.edu.au/miri/research/reports/muarc137.html
[2] http://www.aihw.gov.au/WorkArea/DownloadAsset.aspx?id=6442458828
[3] http://www.monash.edu.au/miri/research/reports/muarc137.html
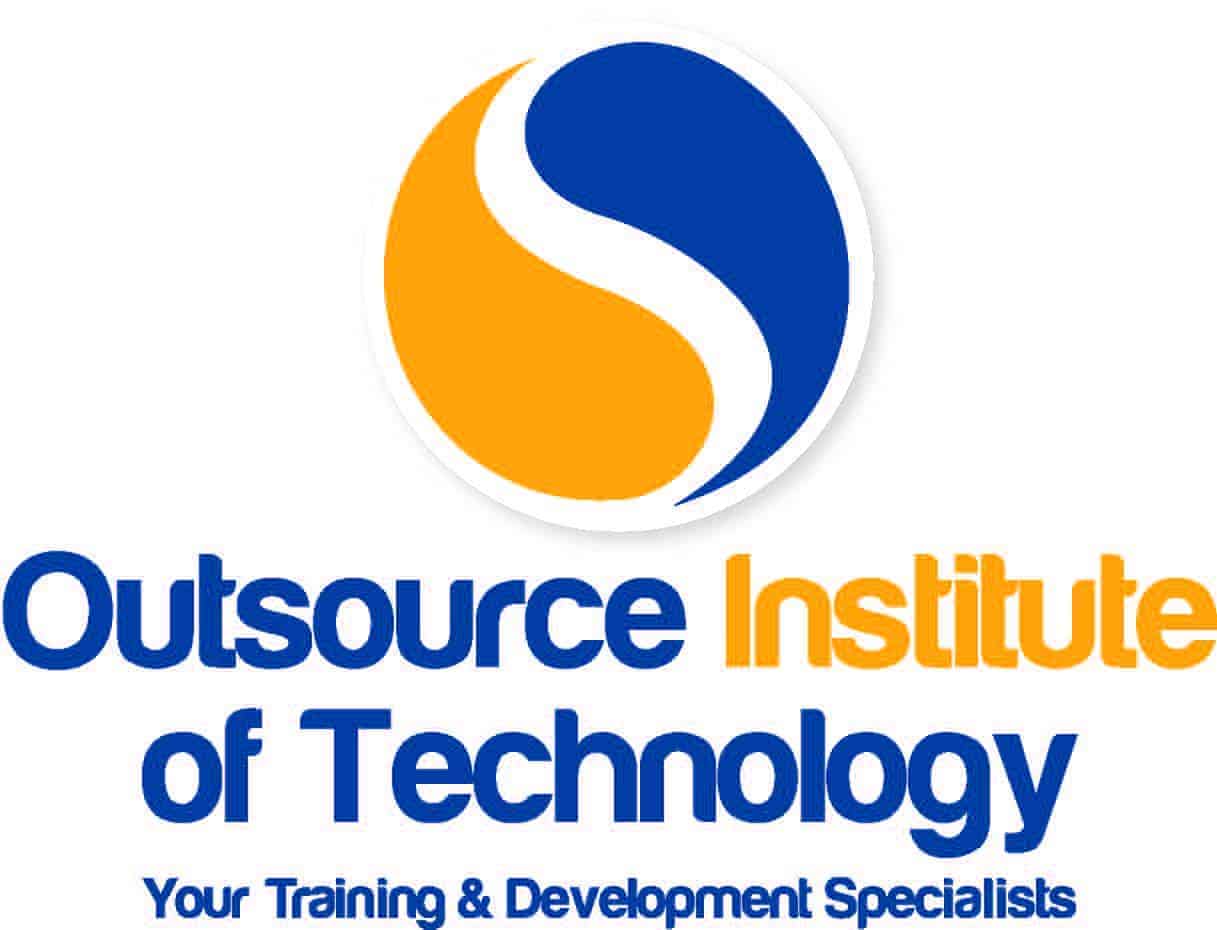
Outsource Institute and AWI
January 1, 2014 in Articles
Outsource Institute of Technology and the Australian Welding Institute (AWITM), have formed a relationship to better serve the industry with the provision of certification for welders and welding supervisors.
Outsource Institute of Technology are grateful for the opportunity to become corporate members of the Australian Welding Institute (AWI). Through the partnership with AWI, they will be delivering AS 1796 Welding Certification courses for tickets 1-9, Welding supervisors to AS 1796 and 2214 and Welding Inspector Certifications.
Outsource Institute of Technology will soon celebrate its sixteenth year of trading as a registered training organisation (RTO). As we travel further into into our second decade we are experiencing our biggest rate of growth since our inception.Our service offerings and professional reputation have gained the attention of an increasingly larger section of industry, in particular mining, engineering, manufacturing and civil & construction.
What sets Outsource Institute of Technology aside from our competitors is that we tailor our training to the client’s requirements, and give learners pathways into qualifications or university that meet their personal needs. Following an extensive RPL process, where we work with our students one-on-one to understand what they currently do, what skills they have, and what gap training they will need, learners are streamline into their course using a fast-track learning methodolgy.
We offer our clients flexible, customised quality training and development services that organisations are embracing, as they are observing the direct correlation between more effective staff performance and increased business efficiency.
Outsource Institute of Technology provides services which are based on competency and business outcome assessment systems, starting with an initial assessment to determine the training needs of your business. We then work with your business concurrently assessing to ensure the training is relevant and effective. Upon completion of the learning program/s, we provide our clients with a final assessment to ascertain the performance improvement of your business and your staff.
Outsource Institute of Technology provides professionally experienced and academically qualified Training & Assessment Consultants to deliver flexible, customised employee training and organisational development services to state, national and international clientele.
Our core business is;
- Flexible Delivery Options
- Business Training Services
- Engineering Training Services
- Customised Training & Development
- Federal and State based funding expertise
- Nationally Accredited and Professional Training Consultants.
Our growth area is in the higher level qualifications particularly for existing workers, to give them mobility within their enterprises and trades, to enable enterprises to develop their staff capability from within, and to equip existing workers with a wider range of skills to meet their job requirements as jobs change with technological advancement.
One key area of concentration for our business is on regional and remote clients (Mining and Construction companies) our goal is to support them with achieving skills that would be otherwise difficult to gain. We offer these opportunties in partnership with industries, other training providers and directly ourselves. When applicable we will also use the recognition of prior learning (RPL) process to acknowledge experience previously gained throughout our clients employment history.
Key Achievements
- First Nation Wide Project – Delivery of the Cert IV in Frontline Management to 15 Field Operational Representatives for Fisher and Paykel. (2003)
- First State Government Contract – Delivery of Cert IV in Frontline Management with articulation to the Diploma of Management for 20 customer service officers at Qld Transport Customer Service Direct call centre. The course was delivered on 2 sites simultaneously using video conferencing facilities linking Brisbane office with Emerald office. Outsource Institute of Technology delivered this course to Qld Transport for 5 years and we have successfully trained 75 Qld Transport staff. (2005)
- First Qld Ambulance Services Project – Delivery of Cert IV in Frontline Management to 22 senior ambulance officers based across south east Qld using a blended face to face and video conferencing delivery mode. (2004)
- Delivery of Diploma of Project Management – to 15 Qld Rail senior staff in Mackay Qld using traditional face to face delivery methods linked to workplace focused project based assessments. (2006)
- First Defence Project – Design, Delivery and Assessment of 14 senior technical staff at Boeing Australia Limited – Amberley Airbase in the Advanced Diploma of Engineering. All 14 staff members have been completed as part of an outplacement project commissioned by BAL.(2007-08)
- First Mineral Processing Project – Delivery of the Advanced Diploma of Engineering to 5 engineering cadets at Ausenco Qld head drafting and design office. The cadets were supported in their learning. (2008)
- First Coal Seam Gas Project – Delivery of the Advanced Diploma of Engineering to 12 engineering cadets at Unidel Qld head drafting and design office using an in-house and external delivery mode. (2009-10)
- First Coal Mine Project – the commencement of 27 Cert IV in Engineering – Fluid Power advanced trade programs to Anglo American Coal in central Qld. The course is a priority one advanced trade apprenticeship designed to train existing tradepeople in advanced trade applications such as programmable logic controlers, hydraulics and pnuematics and hydraulic system analysis. (2011 – concurrent)
- First Pipe Welding Project – the commencement of 5 specialised welding staff in the Cert IV in Engineering – Welding Flemming Welding. The welders were initially RPL’ed for their current knowledge, followed by gap training in welding technology such as metalurgy, welding supervision which will lead to them being able to obtain AS1796 welding certification. (2012 – current.)
- Large Advanced Diploma of Engineering Project – 35 senior technical staff are undertaking the Advanced Diploma of Engineering at Aurizon. We have performed the RPL process and the students are currently undertaking gap training delivered at their sites and vior distance learning processes- (Current)
Our learning management and delivery systems enable us to be a provider of choice as we are accessible to students 24 hours 7 days a week.
In terms of real time business transformation, Outsource Institute of Technology see our innovations in delivery and course offerrings strategically of great importance to us and our clients. Our approach means that clients do not have to travel to Brisbane or other regional centres for intensive training, which enables us to ensure time spent in training can be productive and more importantly cost effective for all concerned.
Outsource Institute of Technology are grateful for the opportunity to become corporate members of the Australian Welding Institute (AWI). Through our partnership with AWI, we will be delivering AS 1796 Welding Certification courses for tickets 1-10 of AS 1796 and Inspector Certifications. If you’re interested in these highly sort after welding certification courses, please log onto www.outsourceinstitute.com.au or call us on 1300 136 904.