History
The correct name for TIG welding is Gas Tungsten Arc Welding (GTAW). This is the name that most European and American Welding fabricators refer to on their welding procedures. When GTAW welding was introduced around the 1940’s, Helium gas was the primary shielding gas used and the term Heliarc welding was in common use, so if you’re going to complete a repair on some old plant from older drawings, you might just happen across this term – welders beware!
Introduction to GTAW (TIG) welding
Manual gas tungsten arc welding is a relatively difficult welding method, due to the coordination required by the welder. Similar to torch welding, GTAW normally requires two hands, since most applications require that the welder manually feed a filler metal into the weld area with one hand while manipulating the welding torch in the other. Maintaining a short arc length, while preventing contact between the electrode and the workpiece, is also important.
What separates GTAW welding from most other welding processes is the way the arc is created and how the filler metal is added. As two hands are required to weld, GTAW welding is the most difficult of the welding processes to learn. It is also the most versatile when it comes to different metals. GTAW is a slow process but when completed correctly, it produces the highest of quality welds. The process is mostly used for critical weld joints, welding metals other than common steel, and where precise, small welds are needed.
To strike the welding arc, a high frequency generator (similar to a Tesla coil) provides an electric spark. This spark is a conductive path for the welding current through the shielding gas and allows the arc to be initiated while the electrode and the workpiece are separated, typically about 1.5–3mm apart.
Once the arc is struck, the welder moves the torch in a small circle to create a welding pool, the size of which depends on the size of the electrode and the amount of current. While maintaining a constant separation between the electrode and the workpiece, the operator then moves the torch back slightly and tilts it backward about 10–15 degrees from vertical. Filler metal is added manually to the front end of the weld pool as it is needed.
Welders often develop a technique of rapidly alternating between moving the torch forward (to advance the weld pool) and adding filler metal. The filler rod is withdrawn from the weld pool each time the electrode advances, but it is always kept inside the gas shield to prevent oxidation of its surface and contamination of the weld.
Filler rods composed of metals with a low melting temperature, such as aluminium, require that the operator maintain some distance from the arc while staying inside the gas shield. If held too close to the arc, the filler rod can melt before it makes contact with the weld puddle. As the weld nears completion, the arc current is often gradually reduced to allow the weld crater to solidify and prevent the formation of crater cracks at the end of the weld.
Power Supply
GTAW uses a constant current power source, meaning that the current (and thus the heat) remains relatively constant, even if the arc distance and voltage change. This is important because most applications of GTAW are manual or semi-automatic, requiring that an operator hold the torch.
The preferred polarity of the GTAW system depends largely on the type of metal being welded. Direct current with a negatively charged electrode (DCEN) is often employed when welding steels, nickel, titanium and other metals. It can also be used in automatic GTAW of aluminium or magnesium when helium is used as a shielding . The negatively charged electro degenerates heat by emitting electrons, which travel across the arc, causing thermal ionization of the shielding gas and increasing the temperature of the base material. The ionized shielding gas flows toward the electrode, not the base material, and this can allow oxides to build on the surface of the weld.[24]
Direct current with a positively charged electrode (DCEP) is less common and is used primarily for shallow welds since less heat is generated in the base material. Instead of flowing from the electrode to the base material, as in DCEN, electrons go the other direction, causing the electrode to reach very high temperatures. To help it maintain its shape and prevent softening, a larger electrode is often used. As the electrons flow toward the electrode, ionized shielding gas flows back toward the base material, cleaning the weld by removing oxides and other impurities and thereby improving its quality and appearance.
Alternating current, commonly used when welding aluminium and magnesium manually or semi-automatically, combines the two direct currents by making the electrode and base material alternate between positive and negative charge. This causes the electron flow to switch directions constantly, preventing the tungsten electrode from overheating while maintaining the heat in the base material.
Surface oxides are still removed during the electrode-positive portion of the cycle and the base metal is heated more deeply during the electrode-negative portion of the cycle. Some power supplies enable operators to use an unbalanced alternating current wave by modifying the exact percentage of time that the current spends in each state of polarity, giving them more control over the amount of heat and cleaning action supplied by the power source. In addition, operators must be wary of rectification, in which the arc fails to reignite as it passes from straight polarity (negative electrode) to reverse polarity (positive electrode). To remedy the problem, a square wave power supply can be used, as can high-frequency voltage to encourage ignition.
Good quality GTAW power supplies come with a feature called a ‘high frequency start’. This eliminates the need to physically strike an arc. Once the GTAW torch is activated the high frequency start feature will create an arc across the gap between electrode and workpiece which creates a brief moment of high voltage. Once the arc is established the voltage drops and the amperage goes to what the machine is set at. This is very useful to keep the tungsten from getting contaminated or adding tungsten into the weld pool.
Some common features for GTAW welding power supplies are pre-flow and post-flow of the shielding gas. The pre-flow feature gives the shielding gas a pre-flow time to shield the weld area before the arc is started. The post-flow feature keeps the gas flowing for a set time after the arc is stopped to keep the molten weld pool protected until the weld cools.
Other features of GTAW welding power supplies are frequency settings that help the characteristics of the welding arc. There are many ways to help the welding arc run smoother. Some of the features do this by using frequency ranges and or pulsing of the welding arc.
The polarity of the welding arc is an important feature. DCEN concentrates approximately 2/3 of the heat onto the workpiece surface, which produces a deep penetration weld. Using DCEP, the reverse occurs, as in 2/3 of the heat is produced within the electrode. This will give a shallower weld which is more suitable for sheet metal and at the same time gives the arc characteristics a cleansing action.
Remote Start vs Manual Start
Once the type of GTAW torch is chosen, there are two options on how to start the arc, manual start vs remote start.
First there is the simple way of manually starting the arc. Just like a MMAW welding once the GTAW welding machine is turned on, so is GTAW torch. The arc is started by manually striking the metal with the tungsten. The second option is remote start. Remote start features come in two different forms, a switch on the torch and operated by foot pedal.
Hand operated remote starts are very simple. All they are is a button that is on the GTAW torch that is simply pressed with a finger once you are ready to start to weld. What happens is the hand operated remote start cable is connected to the GTAW welding power supply and it activates the high frequency start feature. It makes starting the arc easier and keeps the tungsten or the workpiece from getting contaminated.
Foot operated or foot pedal remote starts are a bit more complicated. They control the high frequency start and at the same time control the amperage. Just like the accelerator in your car, the further down you push the more amperage you get. Foot operated remote starts are mostly suited for shop work where the welder is able to sit. It is very difficult to weld standing with a foot pedal remote start. The upside to a foot pedal remote start is you have full control over the heat that you are welding with.
GTAW Electrode
The electrode used in GTAW is made of tungsten or a tungsten alloy, because tungsten has the highest melting temperature among pure metals, at 3,422°C. As a result, the electrode is not consumed during welding, though some erosion (called burn-off) can occur. Electrodes can have either a clean finish or a ground finish—clean finish electrodes have been chemically cleaned, while ground finish electrodes have been ground to a uniform size and have a polished surface, making them optimal for heat conduction. The diameter of the electrode can vary between 0.5 and 6.4 millimetres, and their length can range from 75 to 610 millimetres.
A number of tungsten alloys have been standardized by the ISO American Welding Society in ISO 6848 and AWS A5.12, respectively, for use in GTAW electrodes, and are summarised in the Table 1..
Table 1 Summary of ISO/AWS tungsten electrode classifications | ||||
ISO Class | ISO Colour |
AWS Class | AWS Colour | Alloy |
WP | Green | EWP | Green | None |
WC20 | Gray | EWCe-2 | Orange | ~2% CeO2 |
WL10 | Black | EWLa-1 | Black | ~1% La2O3 |
WL15 | Gold | EWLa-1.5 | Gold | ~1.5% La2O3 |
WL20 | Sky-blue | EWLa-2 | Blue | ~2% La2O3 |
WT10 | Yellow | EWTh-1 | Yellow | ~1% ThO2 |
WT20 | Red | EWTh-2 | Red | ~2% ThO2 |
WT30 | Violet | ~3% ThO2 | ||
WT40 | Orange | ~4% ThO2 | ||
WY20 | Blue | ~2% Y2O3 | ||
WZ3 | Brown | EWZr-1 | Brown | ~0.3% ZrO2 |
WZ8 | White | ~0.8% ZrO2 |
Pure tungsten electrodes (classified as WP or EWP) are general purpose and low cost electrodes. They have poor heat resistance and electron emission and find limited use in AC welding of e.g. magnesium and aluminium.
Cerium oxide (or ceria) as an alloying element improves arc stability and ease of starting while decreasing burn-off. Cerium addition is not as effective as thorium but works well, and cerium is not radioactive.
An alloy of lanthanum oxide (or lanthana) has a similar effect as cerium, and is also not radioactive.
Thorium oxide (or thoria) alloy electrodes offer excellent arc performance and starting, making them popular general purpose electrodes. However, it is somewhat radioactive, making inhalation of thorium vapours and dust a health risk, and disposal an environmental risk.
Electrodes containing zirconium oxide (or zirconia) increase the current capacity while improving arc stability and starting and increasing electrode life.
Filler metals are also used in nearly all applications of GTAW, the major exception being the welding of thin materials. Filler metals are available with different diameters and are made of a variety of materials. In most cases, the filler metal in the form of a rod is added to the weld pool manually, but some applications call for an automatically fed filler metal, which often is stored on spools or coils.
Tungsten Electrode Diameters
The most common electrode diameter sizes (in mm) on the market are:
1.0 |
1.6 |
2.4 |
3.2 |
4.0 |
4.8 |
6.4 |
With GTAW welding the electrode size is not the most critical component of the process. As long as the electrode used stays within its amperage rating. What matters the most is the shape of the tip and that determines the arc characteristics. For most uses any size between 1.6 to 3.2mm electrode diameter will do. Since Tungsten electrodes come in a rod form with a square cut end, an electrode needs to be shaped. Some of the tip shapes used in these electrodes are pointed, rounded, and tapered with a ball end.
Pointed Tungsten Electrodes
A pointed tip is typically used in welding ferrous metals like steel with a DCEN current. This allows the current to flow from the electrode to the metal and tends to concentrate the arc onto the metal. Due to the use of DCEN, the pointed tip tends to keep its shape. If the polarity were reversed the tungsten would likely start melting. Shaping of a pointed electrode is typically done on a grinding wheel or tungsten electrode sharpener. When using a grinding wheel it is best to use a fine grit wheel that is only to be used for sharpening Tungsten electrodes (you don’t want to introduce contaminants onto the electrode). Care must be taken when grinding tungsten. Because of its slightly radioactive nature, you must avoid inhaling any grinding particulate.
To sharpen the electrode point it upward while slowly and lightly rolling it on the grinding wheel between your fingers to obtain a tapered point. If you have a proprietary electrode sharpener, it is much like a pencil sharpener. Much easier and safer as any particulate is usually captured.
Rounded and Tapered Ball End Tungsten Electrodes
Rounded or tapered ball end electrodes typically used for welding non-ferrous metals like aluminium and magnesium. The current used to weld these metals is AC (alternating current). The rounded or tapered ball ended electrode helps by spreading the arc over a wider area of the electrode. To get a round or ball shaped end to an electrode, this it is done using DCEP (direct current electrode positive). To get this shape the Argon gas should be turned on and if possible start an arc on a piece of copper. The tungsten will begin to melt once the amperage is high enough and then start to create a ball shape at the end of the electrode. Once you get the proper size ball at the end of the electrode, stop the arc. After the shape is obtained turn the power supply back to A/C.
In some other cases a rounded or tapered ball end electrodes can be used for welding sheet metals with DCEP. What this does is concentrate 2/3 of the heat on the tungsten electrode and prevent burn through of the sheet metal. With DCEP, avoid too high a welding current, otherwise the tungsten will simply melt.
GTAW Torch Types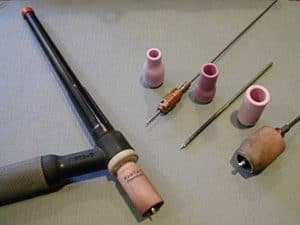
When it comes to GTAW welding there are two options for choosing a GTAW torch! The first is an air cooled torch which is the least expensive and most practical. The down side is the air cooled GTAW torch is it heats up quite a bit and much of the heat the arc produces is wasted.
The second is a water cooled torch. This is the most efficient type of torch but it requires a water cooler and additional maintenance.
GTAW Welding Shielding Gases
Shielding gases for GTAW welding are used to protect the molten weld pool and the tip of the filler wire from the surrounding air which can contaminate the weld. The three most commonly used shielding gases to GTAW weld are:
- Argon / Ar (typically used)
- Helium / He
- Argon/Helium He/Ar mixtures
Since Argon and Helium are inert gases they do not change the characteristics of the weld joint. In some rare cases there are three types of gas mixture used. The first is Argon and hydrogen and the second is Argon and Nitrogen. Helium and Argon/Helium gas mixtures are typically used on thicker metals to get deeper weld penetration. In most cases pure Argon will cover almost all welding needs.
Purging
Purging is a common term when it comes to GTAW welding pipe. The purging of a pipe will replace the air in a pipe with an inert gas that will not react with the root of the weld. Purging prevents weld oxidation. Argon is heavier then air so it will fill a pipe just like water. Typically argon is used to GTAW weld but since it is very expensive it is not always used by itself to purge a pipe. What most people use to purge a pipe is Nitrogen or Co2 gas.
Because argon is a heavier-than-air gas it can be dangerous when proper ventilation is not used. If you are in a sealed room and you have a bottle of argon leaking, it will fill the room from the bottom up, just like water would. Unlike water you cannot see or smell it. Once the Argon fills the room you will be breathing and suffocating at the same time, while not even knowing it.
GTAW Cup Sizes
Cup sizes come with a standard coding system. The coding system is pretty simple! For example a # 5 cup is 8mm or a #9 cup is 15mm.
Filler Wire Designation
Just like any other welding process the filler wire for GTAW welding has a designation coding system. Since GTAW welding does not use any flux, the designations are pretty simple. In most cases you can use MIG welding wire. The only difference between MIG welding wire and GTAW welding wire is the way they are packaged. Typically GTAW welding wire comes in 36” lengths. A common welding wire for mild steel is ER70S-2.
The designation code is as follows:
- ER– An electrode or filler rod that is used in either a wire feed or GTAW welding
- 70– A minimum of 70,000 pounds of tensile strength per square inch of weld
- S -Solid wire
- 2– The amount of deoxidizing agent and cleansing agent on the electrode
GTAW welding wires come in many sizes and these are the more common diameters:
1.6 |
2.4 |
3.2 |
4 |
4.8 |
Joint Cleanliness and Set-Up
Joint cleanliness and set-up is extremely critical when it comes to GTAW welding. Rust, oxidation, mill scale, paint or oil residues will affect the overall finished weld quality giving rise to discontinuities in the weld metal and possible cracking issues. All joints must be cleaned with a grinder or in the case of some metals like aluminium a chemical cleaner is used.
As previously stated, GTAW welding produces a very high quality weld but that weld quality depends a lot on preparation and cleanliness of the joint.
GTAW Welding Machine Set-Up
When setting up a GTAW welder there are two main settings. They are amperage and gas flow. Amperage settings vary depending on the type and thickness of the metal to be welded. Gas flow rates also vary depending on draft conditions, cup size, and sometimes the position of the weld. The gas flow rate could range from 3L/min to 25 L/min for a large cup and drafty conditions. When choosing the gas to weld it is almost always assumed that you will be using pure Argon.
Some basic guidelines for machine set-up are outlined in Table 2:
Table 2 Basic GTAW Set-up | |||
Electrode Size | Typical Amperage | Cup Size | Gas Flow (L/min) |
1.6 | 50 – 100 | 4,5 or 6 | 3 – 8 |
2.4 | 80 -130 | 6,7 or 8 | 4 – 10 |
3.2 | 90 – 250 | 6,7 or 8 | 8 – 15 |
GTAW Welding Stainless Steel
Stainless steel welds almost like steel. It does not take a lot of extra practice, uses the same type of tungsten, and argon gas. The one exception is that welding stainless steel requires good gas coverage. Steel is forgiving when it comes to gas coverage. Stainless steel sometimes requires the weld to be submerged in an Argon bath or if it is an open root weld the inside of the joint must be purged with an inert gas. One of the problems of welding stainless steel is it has a tendency to warp if too much heat is applied or the pieces welded are not braced properly.
Distortion can be controlled by staggering the welds and bracing the weld area frequently. When stainless steel is GTAW welded properly it will have a copper colour to it. If you find the weld to be a gray or dark colour that means either you are moving to slow or your heat input is too high.
When GTAW welding stainless steel, joint preparation is important. The joint must be absolutely free of any impurites. If this is not completed, you will find the filler wire will not flow into the joint and discontinuities will be present (porosity is a prime example). To avoid this it is best to clean the joint with a sanding disk or a file which is dedicated for stainless steel use only. You do not want to introduce carbon steel contamination. This is true on multi pass welds too. If you put in one bead and then need to put in a second pass you also need to clean that area again before welding.
GTAW Welding Aluminium
When GTAW Welding aluminium, there are a few steps needed to complete the set-up. First is the electrode. The tungsten needs to be either pure tungsten or tungsten alloyed with zirconium with a ball shape at the end of it to spread the heat properly. The second is the current type and that is aluminium always welds with A/C (alternating current). Welding aluminium always requires a high frequency start from either a high production button or a foot pedal operated GTAW torch. The main difference when welding aluminium verses other metals is how the puddle looks. Aluminium just has a shiny puddle that does not glow. It looks like tinfoil moving. When welding aluminium, overheating of the metal must be avoided. It is very easy to put too much heat into the workpiece and all of a sudden the whole weld area just drops to the floor.
GTAW Welding Exotic Metals and Alloys
GTAW can weld almost any metal. This is possible because the main gases used are noble inert gases and their properties do not alter the weld properties. Most other welding processes use some type of flux or chemical additives to the filler metal. With GTAW welding it is pure heat that creates the weld joint and that allows any metal that can be melted to be joined as long as the filler wire is compatible. Some of the exotic metals that are commonly welded are:
Copper Nickel and Copper Nickel Alloys
GTAW welding copper and copper nickel alloys are typically done with pure Argon and sometimes Argon / Helium (75% Ar /25% He) gas mixture. In most cases the tungsten type used will be 2% Cerium with an orange color and an AWS classification of EWCe-2. In other cases 2% Thorium tungsten can be used. The most common welding current and polarity is DCEN (direct current electrode negative).
Many people who weld CuNi say it has a muddy feel to it. That is only true if you use too much heat and in that case the metal will turn very dark. When done right the weld will look very close to stainless steel with almost the same copper colour to it. The puddle looks and feels like a combination of stainless steel and aluminium but is more fluid with a hint of shine or tin feel, like welding aluminium. The catch with welding copper nickel and copper nickel alloys is that cold lap and roll are a common problem. Many times the weld looks like it has penetrated properly but in some places it is actually lacking penetration. It is very hard to detect cold roll and lap with copper nickel unless a die penetration test is done.
When it comes to open root welds on CuNi there is a different technique used. To complete good root weld fusion you strike your arc and then create a keyhole followed by stirring and dipping the filler wire into it. You just keep repeating this till the root is finished. It may sound difficult but the filler wire puts in a very smooth root with good penetration on the backside!
Magnesium
Magnesium is typically welded with pure argon gas. The type of tungsten used is typically Zirconiated tungsten with an AWS designation of EWZr. In most cases the current will be A/C requiring a high frequency start.
Titanium
Welding titanium uses argon gas and many times requires extensive gas coverage, usually with a trailing shoe as in most cases the gas coverage that the GTAW cup gives is not enough. Titanium can be welded using 2% Thorium Tungsten with an AWS classification of EWPTh-2 and with DCEN (direct current electrode negative).
GTAW Welding of Dissimilar Metals
One of the less common welding practices is welding of dissimilar metals. GTAW welding has a lot of options when it comes to welding dissimilar metals. Most of these options depend on the design of the filler wire. In a few cases there are two steps to welding dissimilar metals but in the end theses metals can be joined.
Some of the combinations of dissimilar metals that can be GTAW welded are:
- Copper to Silicon bronze
- Copper Nickel to Silicon bronze
- Copper and Silicon bronze to Steel
- Copper to Stainless Steel
- Hastelloy Alloy C to Steel
- Nickel to Steel
- Stainless Steel to Cast Iron
- Stainless Steel to Inconel
- Stainless Steel to Low Alloy or Carbon Steel
GTAW Welding Techniques
When it comes to GTAW welding techniques many of the standard patterns still apply. What really changes is the way the filler rod is added and the fact that you need to use both hands at the same time. When adding the filler rod the filler rod should always be kept in the shielded gas area to avoid contaminating the filler wire. Most of the other changes have to do with how the arc is started. With a high frequency start, the starting of an arc is not an issue. With manual or scratch start there can be some trouble. The main problem with scratch start is that the tungsten may contaminate the weld and lose its shape in the process. The way most GTAW welds are completed is with a side to side motion of the GTAW torch. As long as your amperage is set properly and you see the weld puddle wash into the sides of the weld you should be fine. Just like any other welding process there is not a single pattern or way to make a good weld. GTAW welding works well in all positions on almost any metal. The end result is you want a smooth uniform bead that has washed into the joint properly.
Forehand vs. Backhand
When it comes to forehand vs’ backhanded welding it does not make much of a difference. Since GTAW welding uses a filler metal added by hand, the arc is what determines the weld penetration. As long as the puddle washes into the metal smoothly it makes no difference how you travel. With other welding processes the angle of the travel is unforgiving! GTAW welding on the other hand is very forgiving when it comes to torch angle and travel direction as long as the gas coverage is good.
Freehand
The freehand technique for GTAW welding is exactly that, freehand. It’s pretty simple, just start a weld pool and start adding filler metal with the other hand.
Walking the Cup
Walking the cup is a welding technique that gives the welder a greater degree of control than free hand welding.
When comparing freehand welding to walking the cup there is a huge difference in weld quality and appearance. A weld completed by walking the cup has an almost robot like with the bead pattern very uniform and consistent. This is because the cup of the GTAW torch is always leaning on the weld joint and the arc length is kept the same. Arc length is the key when it comes to GTAW welding bead appearance. To walk the cup you need to place the GTAW torch cup on the weld joint and set the tungsten so that it is just above the weld joint. Then simply walk the cup and add or hold your filler wire in the joint. The cup gets its forward travel speed by moving the GTAW torch handle in a way that creates a forward travel motion. There are many ways to walk the cup but the ultimately it keeps the welder’s hands steady by providing a something to lean on at all times with a consistent arc length.
GTAW Welder Trouble Shooting
When GTAW welding there is some common problems and weld defects. Most of these problems are easy to solve when you know what to look for. Some of the common problems include:
Weld Porosity
Weld Porosity can be caused by many factors. Some of the common causes of weld porosity are:
- Arc length is too long… Shorten your arc length.
- The joint is not cleaned properly… Clean with grinder or wire brush.
- Gas flow rate is too low or too high… In the event of the gas flow rate being too high, the turbulence caused by the high flow rate will pull in surrounding air into the weld pool.
- The wrong cup size is being used… Change cup to proper size.
- Check for a draft coming into the weld area… If this is the case, put up a barrier to stop the draft.
- The filler rod is oily, dirty, or corroded… Try a new filler rod.
- The shielding gas is contaminated… Change the gas.
- The wrong gas is being used… In most cases pure Argon is the proper gas type.
- The hose lines may be leaking… Check connections by using soapy water to find any leaks.
Deteriorating Tungsten Electrode or Unstable Arc
A deteriorating electrode, or an unstable arc is typically due to the following causes:
- Gas flow is too low… Raise gas flow rate.
- Arc length to long… Shorten arc length.
- Wrong gas being used… Change the gas.
- Tungsten is contaminated… Break and reshape the tungsten.
- Tungsten contacted the puddle… Clean tungsten and shorten stick-out.
- Tungsten electrode diameter is too big or small… Replace tungsten with proper size.
- Wrong polarity… Change polarity or voltage type.
- Amperage is too low… Raise amperage.
- Ground clamp is not contacting properly… Clean ground connection.
- Weld metal is not cleaned properly… Grind or wire brush weld joint.
Safety
Welders wear protective clothing, including light and thin leather gloves and protective long sleeve shirts with high collars, to avoid exposure to strong ultraviolet light. Due to the absence of smoke in GTAW, the electric arc light is not covered by fumes and particulate matter as in stick welding or shielded metal arc welding, and thus is a great deal brighter, subjecting operators to strong ultraviolet light. The welding arc has a different range and strength of UV light wavelengths from sunlight, but the welder is very close to the source and the light intensity is very strong. Potential arc light damage includes accidental flashes to the eye or arc eye and skin damage similar to strong sunburn. Operators wear opaque helmets with dark eye lenses and full head and neck coverage to prevent this exposure to UV light. Modern helmets often feature a liquid crystal-type face plate that self-darkens upon exposure to the bright light of the struck arc. Transparent welding curtains, made of a polyvinyl chloride plastic film, are often used to shield nearby workers and bystanders from exposure to the UV light from the electric arc.
Welders are also often exposed to dangerous gases and particulate matter. While the process doesn’t produce smoke, the brightness of the arc in GTAW can break down surrounding air to form ozone and nitric oxides. The ozone and nitric oxides react with lung tissue and moisture to create nitric acid and ozone burn. Ozone and nitric oxide levels are moderate, but exposure duration, repeated exposure, and the quality and quantity of fume extraction, and air change in the room must be monitored. Welders who do not work safely can contract emphysema and oedema of the lungs, which can lead to early death. Similarly, the heat from the arc can cause poisonous fumes to form from cleaning and degreasing materials. Cleaning operations using these agents should not be performed near the site of welding, and proper ventilation is necessary to protect the welder.
Hi I am from Pakistan and I want to ask you that my brother just get his certificate of learning SMAW/GTAW from private institute so it is possible for him to get a job in Australia?